glue uv cured,ultraviolet glue,solder joint protection uv adhesive,glue ultraviolet curing,waterproof uv Dongguan Shuangzhan Industrial Co.,Ltd , https://www.lingwogroup.com
A 4-20mA current loop output serves as a universal standard for testing and diagnosing industrial process control or monitoring devices such as pressure transmitters and flowmeters. Modern instruments like the Rosemount pressure transmitter operate on the Highway Addressable Remote Transducer (HART) protocol, featuring a 2-wire electronic system with a 4-20mA current loop output. This scale is vital for evaluating the performance capabilities of pressure transmitters. Therefore, operators should understand how to test and troubleshoot a 4-20mA signal output. In this post, we’ll explore two methods for testing the 4-20mA current output of a pressure transmitter.
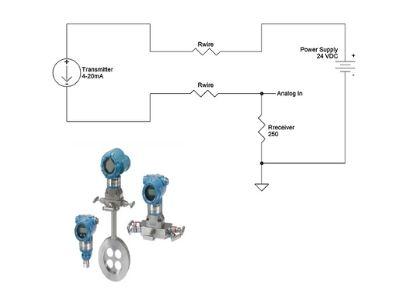
### Understanding the Importance of the 4-20mA Current Loop Output
The 4-20mA signal represents the converted output value generated by a pressure transmitter. Based on the HART protocol, the transmitter's output is transformed into a proportional current to display readings. Typically, a zero-level output corresponds to a 4mA signal, while a full-scale output shows a 20mA signal. Verifying the 4-20mA current loop signals is critical for calibrating and troubleshooting a pressure transmitter. Operators use this scale to configure performance settings.
### Techniques for Measuring 4-20mA Current Loop Output
There are two primary methods used by industrial professionals to measure a 4-20mA current loop output.
#### Method 1: Measuring with a Process Clamp Meter
To measure the 4-20mA current loop output without disrupting the two-wire circuit:
1. Open up the transmitter to access the two-wire current loop and signal wires.
2. Attach the process clamp meter to the signal wires.
3. Check the mA output signals at zero. The reading should fall within the 4mA to 20mA range.
4. If the value isn't in this range, troubleshooting and calibration are necessary. A proper reading confirms the transmitter’s functionality.
#### Method 2: Measuring with a Loop Calibrator or Multimeter
This method involves interrupting the two-wire current loop:
1. Before starting, ensure the pressure transmitter is functioning correctly.
2. Access the transmitter to expose the two-wire loop circuit.
3. Connect the multimeter or loop calibrator in series with the transmitter circuit after disconnecting one end of the signal leads.
4. Set the multimeter to DC measurement mode.
5. Note the mA reading, which should lie between 4mA and 20mA. If not, calibration is needed.
### Professional Testing Services
Performing accurate tests on the 4-20mA current signal requires expertise. Companies like The Transmitter Shop offer high-quality pressure transmitters along with testing and calibration services. With over three decades of experience repairing, calibrating, and troubleshooting both new and surplus transmitters, their services are highly valued in the industry.
### Related Posts
For more insights into pressure transmitters and related topics, check out these posts:
- What are the Steps Involved in Calibrating Pressure Gauge?
- All Important Questions on Reconditioned Transmitters Answered
- Is Remanufactured Transmitter a Better Option than a New One?
And many more! These resources provide comprehensive guidance on selecting, calibrating, and maintaining pressure transmitters effectively.
Wire industry uv adhesive is a one-component, UV Curable Adhesive.solvent free adheisve.it can be cured with in a few seconds under ultroviolet light.After curing UV adheisve has high bonding strength, Mainly used for parallel connection, solder joint protection, cable fixing, bonding of wires and other components, sealing and waterproofing.
Â
Characteristics of UV adhesive in wire industry:
1. Fast curing speed: It can be cured quickly under ultraviolet irradiation, and preliminary curing can usually be achieved within a few seconds to tens of seconds, which meets the production scale of wire rods.
Â
2. High bonding strength: It has good bonding effect on common materials in the wire industry, such as various metals (such as copper, aluminum), plastics (such as PVC, PE, PP) and rubber, and can firmly connect different materials. The wires or wires made of the same material are bonded together with other components to ensure that there will be no glue opening or degumming during use.
Â
3. Good flexibility: After the UV glue is cured, the adhesive layer has a certain degree of flexibility and can adapt to the bending, torsion, stretching and other deformations that may occur during use of the wire, preventing the adhesive layer from cracking due to the deformation of the wire, ensuring good adhesion. long-term reliability of the joint.
Â
4. Good anti-vibration performance: During the use of wires, they may be subject to various vibrations and impacts. UV glue has good anti-vibration properties and can maintain the stability of the bonding between wires or between wires and other components. Not easy to loosen or fall off.
Â
5. Good insulation performance: It has excellent electrical insulation performance and can be used for wire parts that require insulation, such as insulation packaging of wire joints. It can prevent short circuits and leakage between wires and ensure electrical safety.
Â
6. Moisture resistance and waterproof performance: The use of UV glue can effectively prevent the intrusion of moisture, avoid problems such as moisture, corrosion or short circuit in the wire caused by moisture penetration, and protect the performance and life of the wire. It has good moisture resistance and can maintain bonding stability even in high humidity environments.
Â
Â